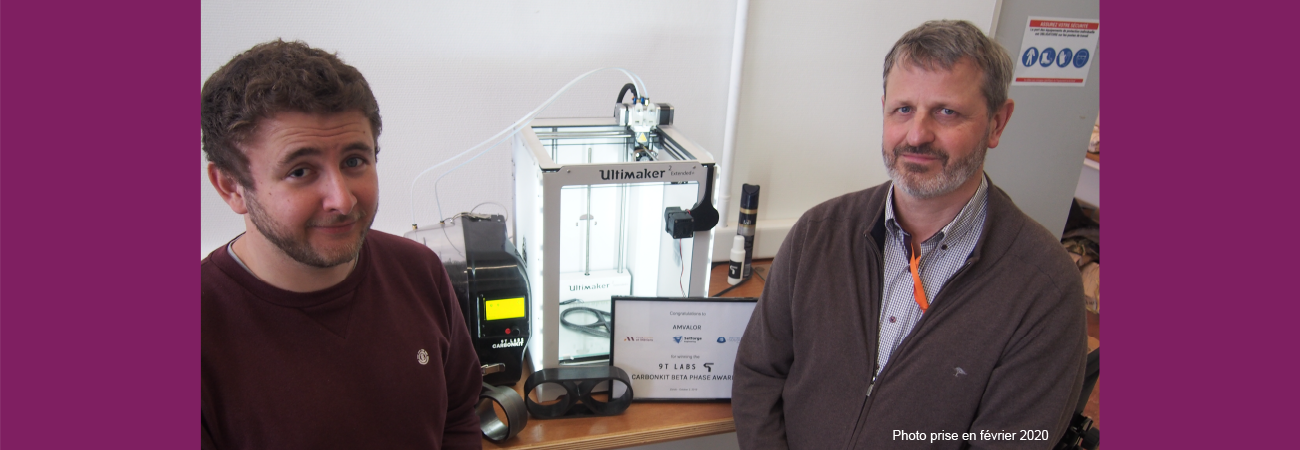
Depuis 2013, le Laboratoire de Conception, Fabrication, Commande (LCFC) du campus Arts et Métiers de Metz développe un procédé innovant de fabrication de pièces massives en matériaux composites grâce à la fabrication additive et à la forge. Un projet innovant mené en collaboration avec AMValor, Setforge (Groupe Farinia) et l’Institut de Soudure Composite Integrity.
Un enjeu environnemental
Les constructeurs automobiles et aéronautiques sont soumis à des règlementations leur imposant de réduire les émissions de gaz à effet de serre. L’une des solutions est d’alléger les véhicules. Pour ce faire, ils réfléchissent à développer les parties structurelles comme les liaisons au sol dans un matériau plus léger, mais tout aussi résistant (élasticité, résistance à la traction, ténacité, etc.).
Si les matériaux composites peuvent remplir ce cahier des charges, leurs conditions de mise en œuvre ne permettent actuellement pas de réaliser des pièces structurelles massives à des cadences satisfaisantes.
D’où l’intérêt de développer un nouveau procédé de fabrication comme le procédé EPITHER sur lequel travaillent le LCFC et ses partenaires. Trois brevets ont déjà été déposés sur ce procédé qui permettra de faire évoluer l’offre des partenaires avec une valeur ajoutée non atteignable par les procédés conventionnels : taux de fibres continues élevées (jusqu’à 60%), très peu de porosités (proche de zéro selon les conditions), aptitude à produire des séries importantes, etc.
Fabrication de la préforme : fabrication additive
Au lancement du projet, les études ont permis de valider sa faisabilité : oui, il est possible de fabriquer des pièces composites massives forgées. Et avec des cadences de production concurrentielles !
Pendant 4 ans, les travaux ont porté sur les différents procédés de placement des fibres pour la fabrication de la préforme : broderie, enroulement robotisé et impression 3D. C’est sur ce dernier procédé que sont aujourd’hui centrées les recherches.
L’utilisation de fibres longues et la maitrise de leur orientation sont essentielles pour obtenir des produits composites très résistants. Une maîtrise obtenue par impression 3D et récompensée par le « Carbonkit beta phase award » décerné en octobre 2019 à Zurich par 9T labs, l’entreprise qui commercialise le matériel permettant l’impression 3D de pièces en fibre de carbone continues et matrice thermoplastique.
Simulation numérique et interactions produit/procédé
En parallèle, ingénieurs et enseignants-chercheurs étudient les caractéristiques du composite massif, c’est-à-dire la santé matière des pièces réalisées (présence de défauts, structure de la matière, orientation des fibres..), mais aussi la manière dont elles réagissent aux sollicitations mécaniques. Pour ce faire, ils s’en remettent au digital en développant des modèles de simulation les plus proches possibles de la réalité.
Les études actuelles portent sur l’interaction produit/procédé : dans quelle mesure les paramètres de fabrication influent-ils sur le produit ? Quelles valeurs permettent d'obtenir une qualité de pièce élevée et stable, reproductible quel que soit le type de pièce ? Ces données serviront à définir sur quels paramètres de fabrication jouer pour obtenir une pièce aux propriétés mécaniques et géométriques attendues.
Des étapes indispensables avant l’industrialisation
Toutes ces étapes sont indispensables avant l’utilisation dans l’industrie du procédé.
En effet, pour produire ses pièces autrement, un industriel a besoin d’assurances : l’assurance que le nouveau procédé lui permettra de respecter ses cadences de production et l’assurance que les nouvelles pièces fabriquées rempliront leur rôle. Pas question d’implémenter dans une voiture ou un avion une pièce qui ne remplit pas le cahier des charges.
C’est là tout le travail des laboratoires de recherche comme le LCFC et de sa filiale de valorisation AMValor.
Les travaux réalisés permettent déjà de réaliser des pièces fonctionnelles. Il est désormais question de mettre en place une ligne pilote qui, en plus de produire des pièces, servira à optimiser le futur outil industriel.
Les publications scientifiques
- Conférence donnée en 2017 au congrès ESAFORM à Dublin « Structural investigation of a new composite process”.
- Travaux de thèse de Philippe Mayer (2018).
- Premier dépôt de brevet en 2011.
- Conférence donnée en 2020 lors d’ESAFORM 2020 à Cottbus en Allemagne : "Forging C/Thermoplastic Printed Composite, Shaping Parameters Impact".