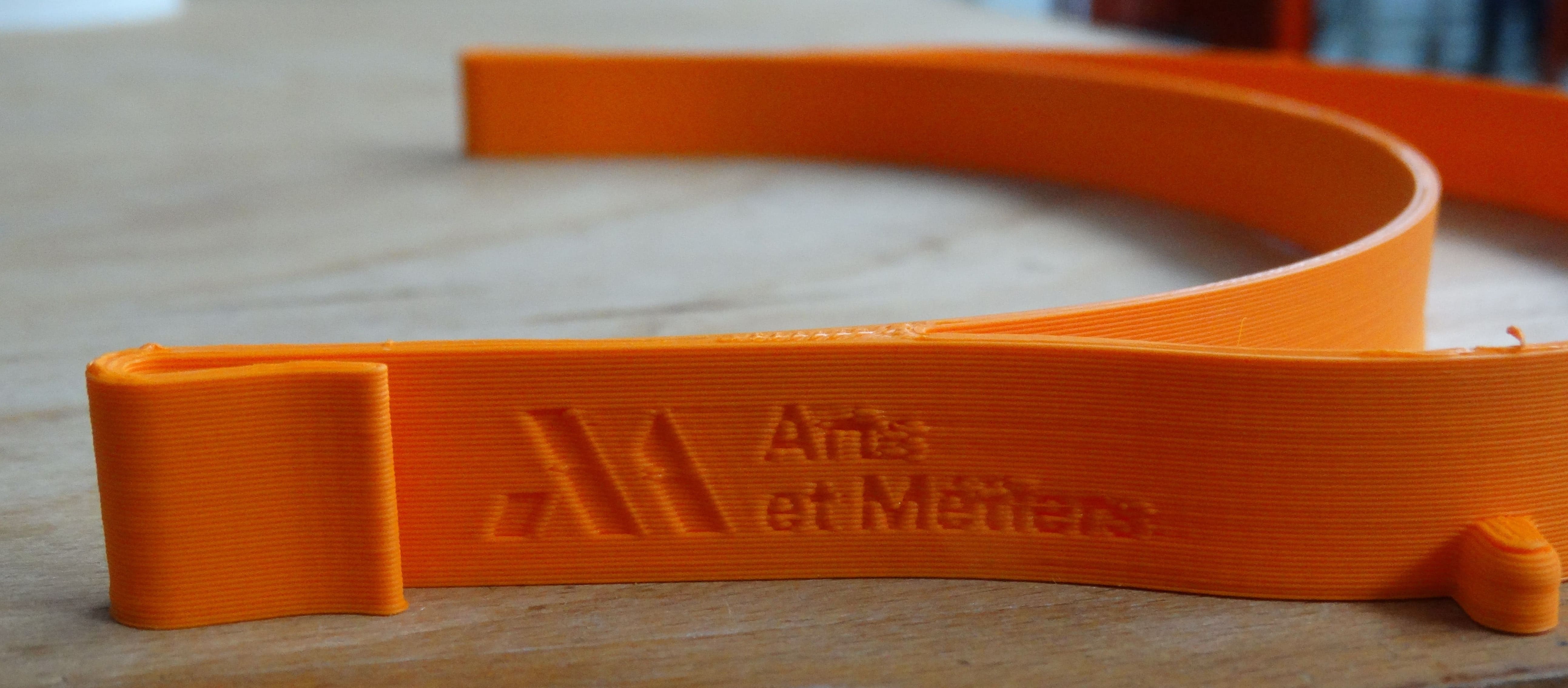
The Covid-19 pandemic is a major worldwide challenge that will ultimately have an impact on our lives for many years to come.
Like many higher education institutes around the world, the Arts et Métiers community is contributing their time and expertise to combat the outbreak.
From the design and manufacture of personal protective equipment to the development of respiratory valves, the Arts et Métiers community is supporting health care staff in hospitals, nursing homes as well as in public services.
Among many of the initiatives, Prof Gilles Regnier, member of the PIMM laboratory in the Paris campus, has designed and mass manufactured injected headband faceshields. On May 5th, more than 9000 faceshields have already been distributed to health care staff.
In the following article, Prof Regnier presents the design and production and discusses how the faceshield can be improved.
Introduction
The rise of the coronavirus responsible for the COVID-19 disease and the social distance it imposes to us has a major impact on our societies.
To support the front-line in care centers and also the second line that ensure sustainability in food and primary goods, technological individual protection solutions, in complement to protective measures against the new coronavirus, are required.
Surgical masks, mostly produced in China, are delivered in priority to hospitals and city doctors. These single use masks have a lifetime of approximately 4 hours, inducing a massive production needs and associated waste disposal of contaminated material. The need for reusable, cleanable and reparable equipment, both for the medical actors and the second line is therefore essential.
The principle of full-head shield, very efficient but expensive and not user-friendly is complex to adapt to a large public, is not the most appropriate to the current emergency.
The use of a face shield, protecting the face behind a sheet of plastic from forehead to chin is simple to protect oneself and others from infected micro-droplets projection. Easy to clean at home with simple soap and repairable in case of a small damage. From this concept, many “Makers” started to produce such shields in their private environment, starting from models in open-access, using their own 3D printers. This led to a regular and local production of hundreds up to thousands of face shields everywhere on the French territory, and across the world.
Yet, as the need is increasing, a more efficient process is needed in order to produce these shields at much higher rates. Cheap, fast produced, condensation free, 4cm away from the face to allow wearing glasses and FFP2 mask underneath, rubber band free and locally produced for reduced logistics is therefore necessary.
Process
3D Printing of face shields
Home printing with personal 3D printers is by far the fastest and most local way to produce and distribute the primary shields, especially with the active and growing community of “Makers”. The additive-fabrication community in Arts et Métiers Institute of Technology moved early and quickly to produce head-bands and distribute them locally. The Arts et Métiers Campus of Bordeaux collaborated with the University Hospital Center to prototype and produce a first model and give open access to the drawings.
Other models that are not requiring a rubber band to hold on to the face, were produced on printers of Arts et Métiers campus of Paris transferred for home office.
Figure 1 : Printable model proposed by Arts et Métiers campus of Bordeaux
Figure 2 : Model printed at Arts et Métiers campus of Paris. A- printing process. B series of face shields prior to distribution
Gearing up to mass production
The adaptive nature of 3D printing and its wide diffusion in public infrastructures or Makers community allowed a fast and precious primary reaction for the first line. Yet, the massive need and the end of the generalized quarantine means there is a need to massively increase production, and 3D printing is expensive and slow (more than an hour per head-band).
The most adapted technology to industrial production of plastic equipment of this nature is thermoplastic injection molding. The principle is to inject at high pressure some high viscosity melted thermoplastic mater in a mold. Production time decreases to 30 to 40s per head-band!
Figure 3 : Mold imprint fabricated at the Arts et Métiers campus of Bordeaux. A, B : machining steps. C: final imprint for injection
To face increasing demand, the Arts et Métiers campus of Bordeaux rapidly produced internally a mold. In the meantime, in the Ile-de-France region, the Institut Universitaire Technologique of Cachan was amongst the first to produce an injection mold on the 6th of April to support the dispensing platform 3D4Care (https://www.3d4care.com/). This mold was mounted on the injection molding press of the PIMM laboratory and the members of the lab took turns for 5 days to produce 1450 head-bands made of polypropylene for 3D4Care and 300 for direct orders to Arts et Métiers.
Figure 4 : Head band model by injection, produced at the Cachan IUT. A final imprint of the production mold. B fully functional face shield
Geometric model conception
Because of the increasing demand, Prof. Gilles Régnier from Arts et Métiers campus of Paris was also requested to coordinate the development of an injected headband model.
Figure 5 : printed model of the model developed at Arts et Métiers campus of Paris
A hybrid model, designed on Autodesk® Fusion360, is using the front part of the PRUSA open-source model validated by the 3D4Care association and in partnership with public health agencies and hospitals. This model keeps a 4 cm distance between the user’s forehead and the glass shield, thereby leaving room for for glasses and a mask. The top part is open to avoid condensation and the forehead support remains flexible for maximum comfort throughout a day of work. The branches are based on a 3DVerkstan model. This last model is printed in large numbers and is widely acknowledged by the clinicians. Wearable without a rubberband and easy to disinfect, the branches still allow rubberbands for specific operations in hospitals. The back-side of the branches have been adjusted in order to be able to use a 12cm long rubber-band for the cases where clinicians require it.
Figure 6 : Rheological simulation of mold filling to optimize geometry and injection parameters
To respond to a reinforced protection request, a secondary half-sheet can be added upwards. 3D printed prototypes allowed to validate all these functionalities (fig. 5). Self-standing on the forehead is validated with material having a Young Modulus greater than 2,5GPa. The current 3D printed head-band made of PLA weighs only 27g.
Figure 7 : Geometrical model developped at Arts et Métiers campus of Paris
Conception and creation of the mold
Once the functionalities were validated, shapes and thickness were optimized by rheological simulations (fig 6). A pressure of 380 bars is required to fill the mold cavity in 1 second using a polyamide 6.
Figure 8 : Model and mold for injection with automatic part ejection for a continuous production plan
Starting from the validated geometry (fig 7), Jérôme Heiligenstein from CryoCapCell, a company hosted on Arts et Métiers campus of Paris, conceived the mold with automatic ejection of the parts to allow automatic production (fig 8). The mold was manufactured in less than 5 days by Barbier MGO near Clermont-Ferrand, based on a mold frame kindly provided by CryoCapCell. The mold was mounted on April 20, 2020 on the DK Codim 175-400 injection Press of PIMM laboratory at Arts et Métiers campus of Paris (fig 9). In one week, 2600 face-shields made of polyamide 6 and weighing 22.5g were produced at a cycle rate of 40s. The 2600 face-shields have already been packaged and distributed to the customers.
Figure 9 : Production at the laboratory. A Injection press of the PIMM. B Head band injected in polyamide 6. C- production session. D- Face shield in use. E- hourly production of head-hand
Discussion
The proposed model is one of many already proposed by academics and industrials since the beginning of the epidemic crisis in France and in the world. Among the improvements already proposed on the headband presented in this article, it would be wise to increase the branches rigidity by thickening them from 6.5mm to 7.5mm. Narrowing the shield arc closed to the user’s face by 5mm on each side would also better tighten the shield around the face, improving its efficiency.
After one week of production, it appears useful to increase draft angles in the mold by 3° to improve the part ejection.
The geometrical model is available on the PIMM laboratory website, and the mold’s drawing is available upon request at contact@cryocapcell.com
Last but not least, note that the GINETIS association lists and distributes all open-source initiatives imagined by the various actors of the national production
Acknowledgements
- Pierre Lapouge for the PRUSA geometrical model datasets, printed by the 3D4Care facility,
- Xavier Bonnet and Alexis Thézé for printing the prototype that allowed to validate the head-band design,
- Loic Verseau from DIAM company and his suggestions on the faceshield conception
- Raw material donators so far: Arkema, Bureau Vallée, Toray,
- Gaëlle Minard who is organizing supply and production as well as all the members of the PIMM laboratory who volunteer to come out of quarantine and help produce faceshields.
Authors
Catherine Desnaives, Barbier MGO
Paulo Ferreira, Arts et Métiers
Jérome Heiligenstein, CryoCapCell
Xavier Heiligenstein, CryoCapCell
Pascal Martinelli, IUT/Hublex
Sylvain Persohn, AMVALOR
Gilles Régnier, Arts et Métiers
Contacts
Arts et Métiers : gilles.regnier@ensam.eu / gaelle.minard@ensam.eu
CryoCapCell : contact@cryocapcell.com